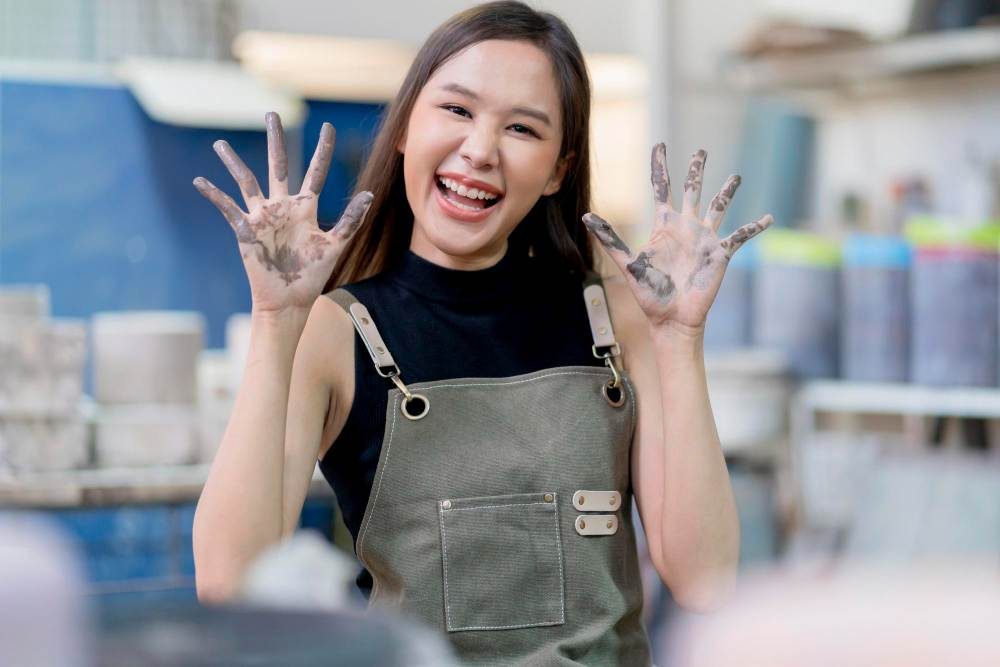
The Most Effective Warehouse Layout for Efficiency
Optimizing warehouse operations in today’s fast-paced business environment is critical for ensuring smooth supply chain management. The foundation of an efficient warehouse is its layout, a vital component that influences productivity, safety, and operational costs. This article explores strategies for creating the most effective warehouse layout and addresses common questions to guide you toward better warehouse management.
Introduction to Warehouse Layout Design
Warehouse layout design involves organizing storage areas, inventory zones, and pathways to enhance operational efficiency. A well-planned layout directly impacts the speed and accuracy of order fulfillment, making it a cornerstone of effective logistics.
Importance of an Effective Warehouse Layout
Enhanced Productivity
A streamlined layout minimizes the distance workers travel to retrieve or store items, thereby increasing throughput. Clear pathways and organized storage zones ensure smooth workflows and reduce congestion.
Cost Reduction and Space Optimization
Utilizing vertical storage, compact shelving, and smart zoning can maximize usable space. An optimized layout reduces wasted space and lowers costs associated with inefficient operations.
Improved Safety Standards
A safe warehouse minimizes accidents and protects employees. Effective layouts incorporate wide aisles, proper lighting, and designated pathways for forklifts to ensure safety.
Key Factors to Consider in Warehouse Layout
Storage Requirements
Determine the types and volumes of inventory you handle. High-turnover items should be stored near dispatch areas, while low-turnover items can be placed in less accessible zones.
Inventory Management Systems
Integrating automated inventory systems can guide layout planning, ensuring compatibility with modern technologies.
Workflow Patterns
Understand the flow of goods from receiving to dispatch. Align storage areas and pathways with these patterns to eliminate redundancies.
Types of Warehouse Layouts
U-Shaped Layout
The most common and efficient design, the U-shaped layout organizes receiving, storage, and dispatch areas in a U-formation. This layout minimizes travel distances and simplifies workflows.
L-Shaped Layout
Ideal for smaller warehouses, this layout uses perpendicular zones to separate processes, optimizing space while maintaining efficiency.
Grid Layout
A flexible design that works for warehouses with diverse inventory types, the grid layout facilitates easy navigation and organization.
Steps to Designing the Most Effective Warehouse Layout
Assessing Space Requirements
Conduct a detailed analysis of your current and future storage needs. Consider seasonal fluctuations and potential business growth.
Planning for Scalability
Design a layout that can accommodate expansions or changes in inventory patterns without major disruptions.
Incorporating Technology
Adopt automated picking systems, RFID tagging, and other technologies to enhance the efficiency of your layout.
Best Practices for Warehouse Layout Optimization
Zoning and Segmentation
Divide the warehouse into distinct zones based on inventory type, turnover rate, and storage requirements.
Flexible Shelving Systems
Invest in adjustable shelving to adapt to changing inventory sizes and volumes.
Lean Layout Principles
Eliminate unnecessary steps and redundancies in your layout to streamline operations and reduce waste.
Common Challenges in Warehouse Layout Design
Handling Irregular Inventory Patterns
Fluctuations in inventory levels can disrupt workflows. Design a layout that can handle such variations seamlessly.
Managing Seasonal Demand
Plan for peak seasons by incorporating temporary storage areas or scalable shelving systems.
Adapting to Technological Changes
Keep your layout flexible to integrate new technologies without overhauling the entire system.
Conclusion
An effective warehouse layout is the backbone of efficient operations, driving productivity, safety, and cost savings. By understanding your storage requirements, integrating technology, and planning for scalability, you can create a layout that supports your business goals.
FAQs
1. What is the most effective warehouse layout for small spaces?
The U-shaped layout is often the best for small spaces due to its efficient use of available area and streamlined workflows.
2. How does technology influence warehouse layouts?
Technology such as automated picking systems and RFID tagging helps optimize storage zones and streamline processes.
3. What factors should I prioritize in warehouse layout planning?
Focus on storage requirements, workflow patterns, and the integration of modern technologies.
4. Can warehouse layouts be redesigned for scalability?
Yes, a well-thought-out design considers future growth and allows for easy expansion.
5. What safety measures should be included in a warehouse layout?
Ensure clear pathways, adequate lighting, and designated zones for equipment to maintain a safe working environment.
Want to learn more? Read: https://medium.com/@hasibul_8488/how-to-design-warehouse-layouts-for-retail-marketing-and-rental-spaces-d213569d682d